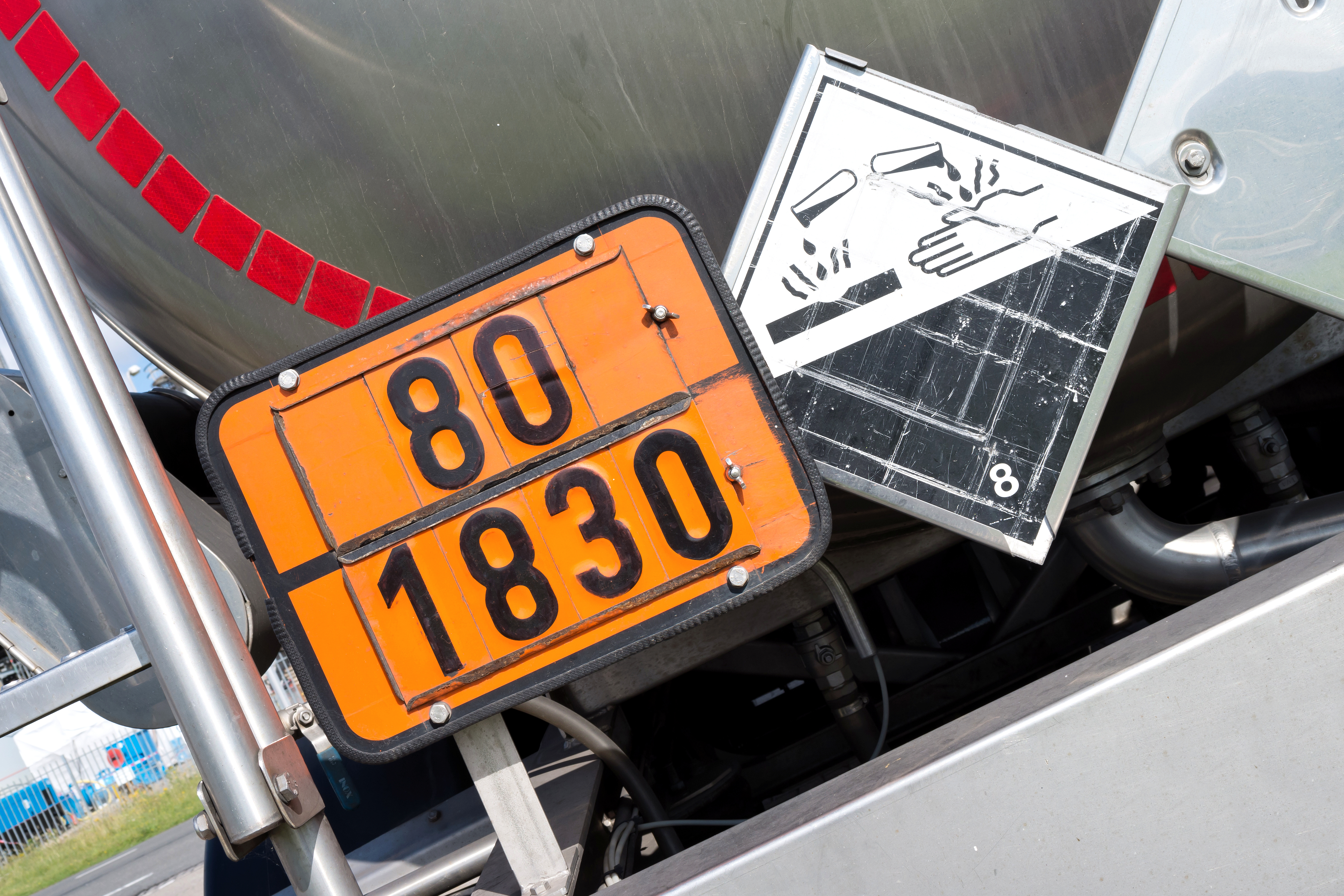
In the event of a fire inside a tunnel, the dispersion of gases and heat is prevented, creating extreme temperatures that have led to many deaths. Following tragic incidents including Mont Blanc, European legislation requires longer tunnels to be fitted with incident and smoke detection systems.
Such standards have been adopted well beyond the EU’s borders and many countries go well beyond the specified standards. Sweden, for example, has implemented camera surveillance in almost all long tunnels, including the Norra Länken (Northern Link) motorway in Stockholm.
Here, the authorities worked with Swedish integrator
Enforcing such bans is challenging but remains necessary, as each year, trucks are caught ignoring signs. Governments and road authorities have sought technological ways to monitor trucks entering tunnels not only to detect and fine transgressors but also to know what potentially dangerous goods may be in the tunnel at any one time. This information can be used to enact the correct emergency procedures, such as using foam rather than water to fight chemical fires.
French integrator
Its systems use two Sony FCB cameras to detect the dangerous material signage and the number plate, and the system instantly sends an alert to digital road signs by the tunnel entrance directing drivers to either turn back or continue. Once in the tunnel, vehicles can be tracked using a series of cameras.
Technical considerations
ITS applications are very challenging, requiring sharp images of moving vehicles and near-instant analysis. In a tunnel situation, the cameras outside the entrances have to cope with extremes of light and fast-changing light levels, while those inside tunnels need to produce high quality video for algorithms despite being in a low-light environment subject to shadows and headlight glare.
Traditionally, with fast moving objects, the exposure time was reduced by setting exposure times for the brighter areas of the image or by increasing the image sensor’s light sensitivity. But this often leads to glare in another part of the image and while image processing can partially correct problems, the increased computational load slows the system and makes it harder to distinguish real defects from illumination artefacts.
CMOS sensors provide a wider dynamic range but the traditional rolling-shutter means not all parts of the image of the scene are recorded at precisely the same instance, so fast-moving vehicles are subject to blurring effects. While the sensors can be overclocked (to run at up to 120fps), highways agencies have almost exclusively adopted GigE due to its long transmission range, but it limits data transmission to 1Gbps. This equates to approximately five megapixel images at 24fps.
Many of the latest CMOS sensors have global shutters which capture complete frames in the same instant to counter blur and provide exposure control at the pixel level to optimise illumination consistency.
Capture settings
In a tunnel where transmission distances can be relatively short, wide dynamic range techniques such as taking multiple shots in very quick succession, differing only in exposure times, can be use. Merging these images enhances dark areas and reduces glare in bright sections to optimise the image and create a sharper picture free from blurring and heat shimmer. Again, this creates large file sizes but with ITS applications it is possible to focus on regions of interest by programming the image sensor to send only portions of an image, and thereby optimise the available bandwidth.
ITS vision systems are evolving, utilising deep learning and analytics to monitor the way people are driving. It is likely such systems will be soon be implemented in high-risk environments such as long tunnels, to identify erratic driving and other issues such as overloaded vehicles.
As camera evidence is used in legal proceedings, there is a need to identify who is driving and so advances in polarised-light sensors are likely to make their way into ITS cameras. These further reduce glare, making identification easier, even in challenging and high-risk environments.