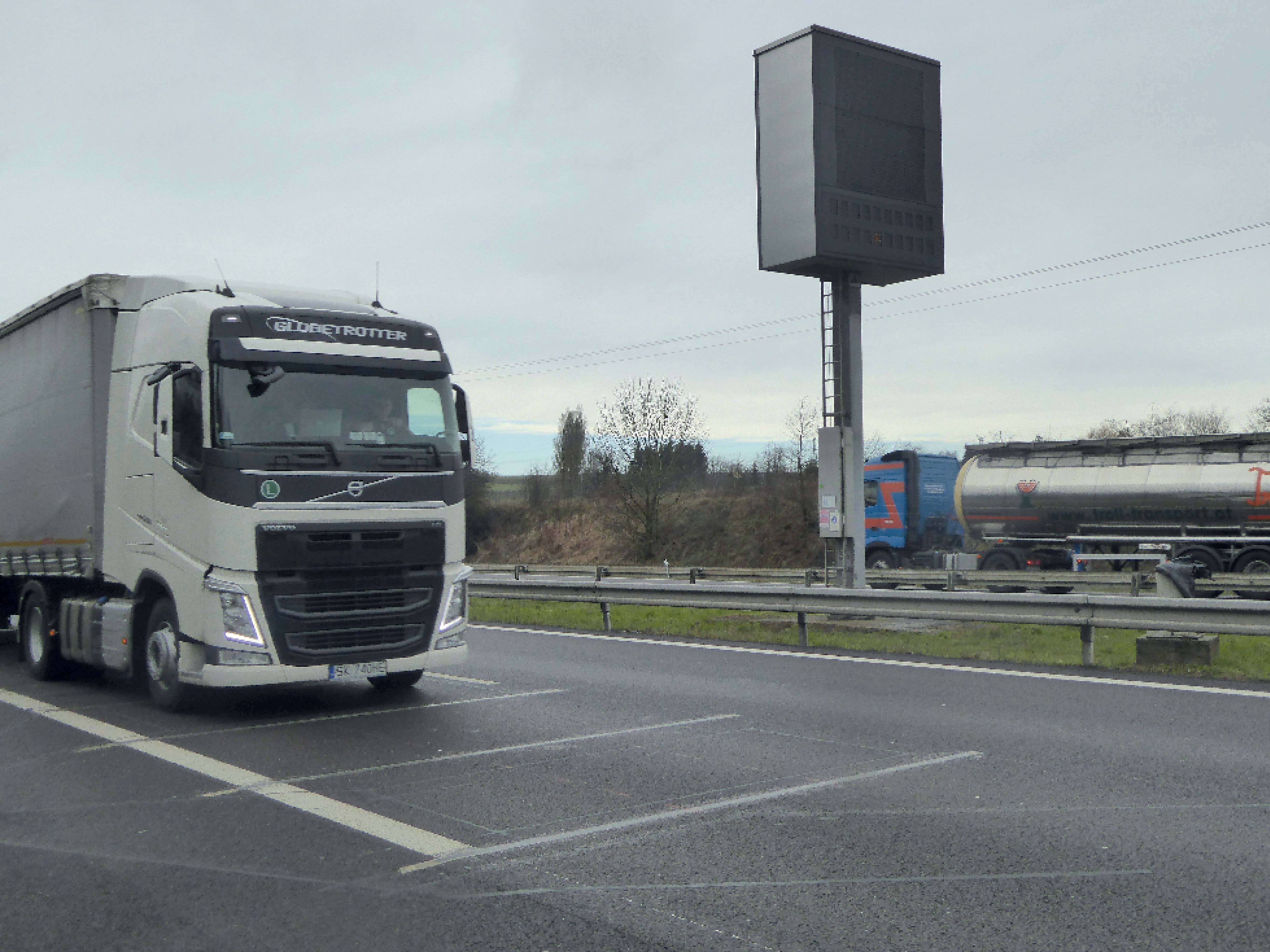
High-speed weigh-in-motion is starting to make its mark on both sides of the Atlantic.
As a transit country the Czech Republic experiences a large number of overloaded vehicles, which greatly increase highway maintenance costs. This prompted its Transport Ministry to trial an extension of the capabilities of the existing truck tolling system to allow the dynamic high-speed weighing of cargo vehicles. In effect the tolling enforcement gantries become weigh-in-motion (WIM) locations.
In 2012 the country modified regulations to enable direct enforcement without static weighing (provided certain performance parameters were met) and initiated a four-year trial of the technology. Five pilot projects were set up – each with different equipment suppliers and in 2014, before the pilots had concluded, the government announced plans to deploy 15 dynamic weighing systems in the proximity of border crossings to monitor transit traffic entering the Czech Republic.
One of those Direct WIM enforcement pilot projects was undertaken in association with
The high-speed WIM sensors can weigh all the vehicles that to pass over them in normal traffic conditions and as overweight vehicles no longer need to be weighed statically, the system offers significant efficiency gains. These include reducing the workload on the enforcement agencies to allow them to concentrate on safety issues. The data collected can be used to feed pavement management systems (to optimise repair and maintenance planning) and reinforce road safety and, in this instance, monitor international traffic load on transit roads to obtain EU funding.
Legal Framework
The Technical Decree which implements the Act’s details not only lays down the technical standards but also grants legal authorisation to access the central vehicle register in order to identify the overweight vehicle’s owner/operator.
Technically such systems require type approval to the standards set out in the technical decree which specifies that weighing accuracy must be within 5% across a speed range of 10km/h to 160km/h and a control system capable of recognising internal faults. External problems (extreme weather conditions such as snow and ice, lightning and carriageway contamination) or sudden vehicle manoeuvres (acceleration, deceleration) may be beyond the scope of the monitoring system.
As the tested WIM systems did not meet the 1cm accuracy criteria for measuring the distance between the axles at highway speeds, individual axle weights could not be enforced and action was only taken when the permissible total vehicle weight was exceeded. Technical changes to the legislation will make it possible to determine the weight of a group of axles without the precise measurement of the distance between the individual axles. However, the corresponding maximum weights may not be available on the vehicle register.
It is also necessary for the system to measure vehicle speed with an accuracy of 1% and to meet the legislative requirements regarding the capture and storage of information (date, time, place, speed, total weight, number plate and photographs) for enforcement purposes.
Pilot Results
The pilot in which Kapsch was involved used sensors installed in one lane of the I/52 road in Modice near the Moravian metropolis of Brno. It was deployed into the toll system and used as part of the toll-collection enforcement process which charged the overweight vehicles through the tolling system. In the first eight months of operation data was collected on 435,346 vehicles over 3.5tons of which around 68% were weighed with 100% validity. Over that period the standard deviation of the measurements was 1.1%.
Of the 32% of invalid measurements, many were due to the way the vehicles were driven (deliberately or not) with wheels in adjacent lanes (which were not fitted with weight sensors) or the drivers zig-zagged, braked or accelerated. The system identified, assessed and eliminated most non-linear behaviour using corrective algorithms and in any future installations the use of three sets of sensors across adjacent lanes would significantly improve the proportion of useable readings.
Almost 6,900 (or 1.58%) of the heavy vehicles passing over the sensors registered as overweight but around 5,100 had an overweight axle. Only 1,791 exceeded their permitted total weight and of those 1,218 could be fined for being 1tonne or more over the allowable weight (plus the 5% tolerance). If the operator was charged 7,000 CZK (€258/$281) for each tonne of overweight - the average overload was 3tonnes (therefore would be charged as 2tonnes) – this would, if executed, generate a total income exceeding €900,000 ($978,000).
In the following year some 616,296 vehicles above 12 tonnes passed over the pilot installation of which almost 13,000 (1.8%) were overloaded.
Based on the initial findings, the installation’s payback period would be about four months but, more importantly, experience shows that heavy vehicle operators take measures to prevent overloading when they know they will be detected and fines levied. In that way the road damage, which can take seven years off the life of a road with a design life of 20 years, can be avoided on routes beyond those fitted with WIM sensors.
Currently the Czech Republic’s plans for 15 direct WIM enforcement locations are being delayed by internal political matters but France and Poland are considering installing similar systems. It is likely any direct WIM enforcement legislation in these countries would have tighter tolerances – potentially within 1%. What is perhaps more difficult would be meeting the 1cm accuracy requirement for measuring the spaces between the axles for the individual axle weights calculations.
Efficiency upgrade
There are similar moves across the Atlantic where the US state of Georgia has 19 roadside weigh stations located on key routes and drivers of vehicles over 10,000lbs (approximately 4.5tonnes) must pull into all open weight and inspection stations.
While the weigh stations have WIM ramp sorting to speed compliant trucks through the station, highway backups can occur and manpower requirements are relatively high.
To increase efficiency and extend the life of small weigh stations with a limited throughput capacity, many US states are looking to technology upgrades such as remote operation and Virtual Weigh Stations. The remote operation boosts efficiency as it allows multiple sites to be managed from a central location while Virtual Weigh Stations are used to catch drivers attempting to bypass stations by taking another route.
Against this background, the Georgia Department of Transportation (GDOT) decided to augment the existing ramp sorter systems in its weigh stations by installing high-speed weigh-in-motion to the main highway and adding e-screening capabilities. There is also a desire to better target enforcement without impeding compliant vehicles and operators.
This combination of high-speed WIM on the main highway and e-screening will both increase enforcement efficiency, as all vehicles using the road will be weighed, and allow a greater focus on high-risk and/or non-compliant carriers. It also allows compliant vehicles and drivers to keep moving (and thereby minimise or prevent backups with their attendant safety risks), save time, fuel, emissions and vehicle wear.
International Road Dynamics (
As a vehicle passes over the scales, the WIM system collects axle and gross vehicle weights, axle spacing, vehicle length and speed, enabling the system to determine the vehicle’s weight classification and compare the measured weights with the class maximum.
At the same time the vehicle’s license plate is automatically read and the USDOT number on each vehicle is read and checked against the state database for weight, credential and safety issues. A third camera takes an image of the truck and the system creates a vehicle record consisting of the vehicle’s weight and dimensions, date and time, over-height information, lane number, potential violations and photographs. The sort decision (report or bypass) is then made and communicated to the driver in real time using changeable message boards positioned close to the ramp exit.
In operation the WIM system is working well although the e-screening has not yet been activated. Ultimately GDOT plans to share data from the enforcement sites across other departments, making traffic data available for research and planning.