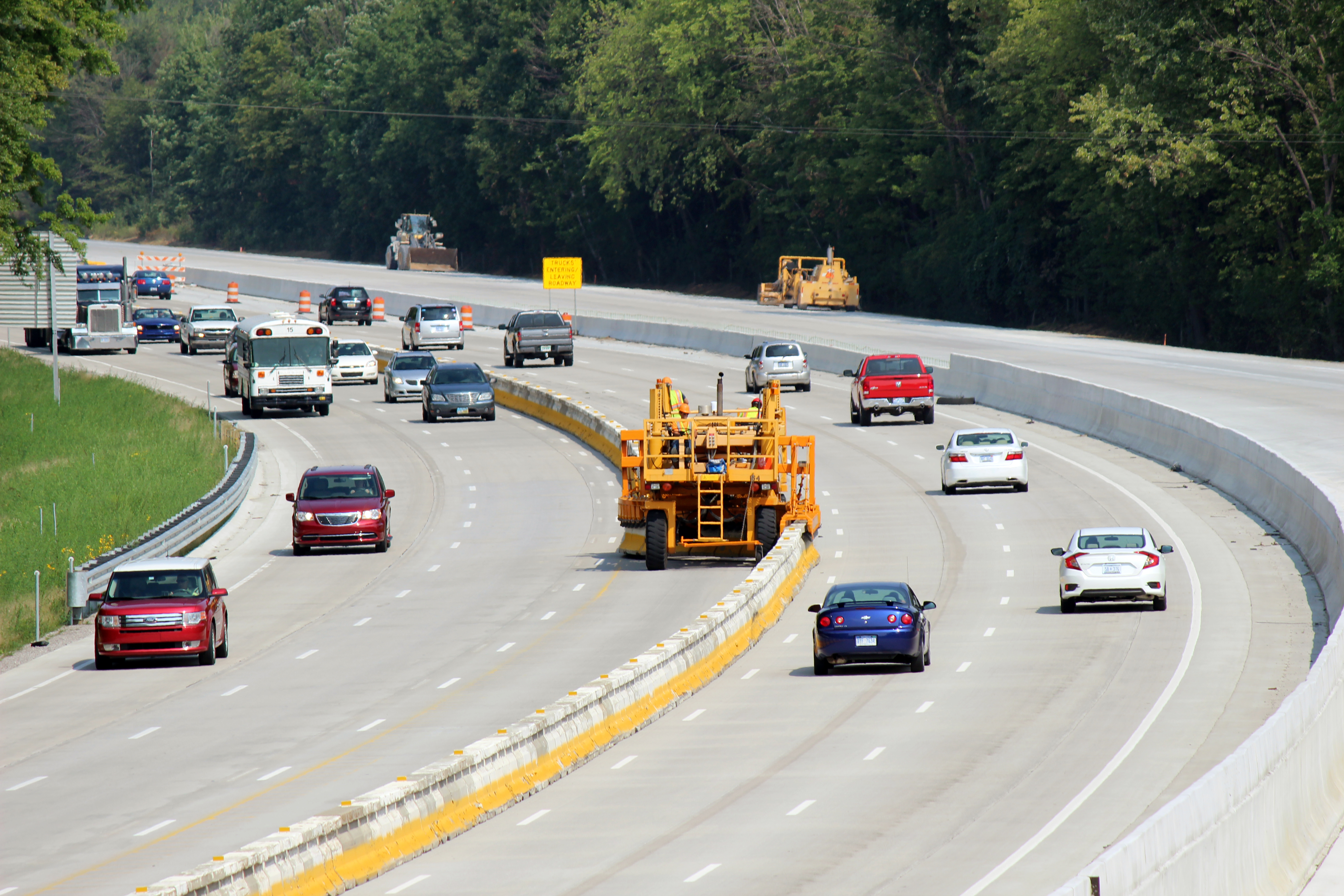
Moveable barrier systems are offering engineers a new traffic management options.
Work zones - be they for maintenance or road widening - are a fact of life and when they occur on major highways, they create no end of problems for traffic planners and travellers alike. ITS can help minimise the inconvenience for drivers and enhance safety for road workers – but the intelligence does not start and end with electronics systems finding the best compromise within the fixed road infrastructure. In these situations the number of available lanes through the work zone may simply not be appropriate for the volume of traffic – or at least not in the right direction. This capacity mismatch not only occurs in work zones but also with big variations in traffic volumes - tidal flows into cities in the mornings and away from the cities in the evening.
ITS can help with programmable and adaptive traffic lights but there comes a point when it becomes necessary to consider temporary reconfiguration. Contraflows invariably mean a loss of lanes and simultaneous disruption to both sides of the corridor while reversible lanes can ease the congestion caused by tidal flows – but these may require additional land.
Temporary reconfiguration using moveable barriers, such as
Having lifted the barrier sections off the ground, the BTM moves forward and the sections pass through a conveyor system before being placing back on the ground in the new position - somewhere between 2.4m and 7.3m (eight to 24ft) to the left or right. A water-filled Absorb 350 crash cushion is pinned to the final block at each end of the chain. The NCHRP350-tested cushion provides protection at up to 100km/h (62mph) and also comes with a ‘T’ shaped top so it too passes through the BTM with the barrier sections to minimise reconfiguration times.Key benefits of moveable barriers tidal flow:
• Positive protection from oncoming traffic eliminates crossover crashes
• Only 10-20% of the cost of adding a new lane
• Speeds implementation compared to new construction
• Improves commuter travel times and fuel efficiency
• Adapts easily to changing traffic patterns and commuter needs
• Operates in all weathers
The BTM has a working width of 4.4m (14ft 5ins) and hydrostatic drive provides a 32km/h (20mph) a travel speed and up to 18km/h (10mph) working speed. When being moved between sites, the machines has manageable transport dimensions of 2.6m (8ft 6ins) wide by 15m (49ft) in length and it weighs 19.3t (42,550lbs).
These moveable barriers are increasingly being used in a number of ways within both work zones and for temporary, or even permanent but moveable, road configurations.
Work zones
In Central Michigan, the busy five-lanes in each direction I-75 corridor also experiences heavy weekend tourist traffic, so repair work on a 6.1km (3.8miles) section which closed one of the carriageways, could easily have brought traffic to a standstill. Traditional contraflows with temporary concrete barrier to separate directional traffic would mean restricting traffic to a 3/2 pattern through the duration of the $46million project.Instead, MDoT used the Road Zipper’s moveable barrier to keep three lanes open in the peak direction at all times while retaining positive barrier protection between opposing traffic lanes.
The barrier provided three lanes north Wednesday through to Saturday, and three lanes south Sunday through to Tuesday. Switching from one configuration to the other took about 30 minutes without the need to temporarily stop the traffic during the switchover.
After the project finished in September 2016, MDoT estimated this way of operating saved $30 million in user delay during the construction season. Region manager Robert Ranck says one of the reasons for selecting the moveable barrier system was to give drivers a safe, confusion-free path through the work zone. “As the wall is being moved, traffic is running at a normal pace, and [drivers] only notice that a lane just opened or closed, so it’s the safest possible way to do the work.”
This fact, coupled with the advent of portable VMS, means adhering to the applicable signage standards is not difficult even with the dynamic nature of the road layout. A similar approach is being taken in Denmark on a 5km (3.1miles) stretch of the Koge Bugt Motorway leading into Copenhagen city centre. In its standard configuration the highway has four lanes in each direction and last year the ongoing road works resulted in unacceptable traffic queues due to the loss of traffic lanes.
During the works (which are divided into 5km segments), a static barrier is typically placed on the construction side, reducing the available traffic capacity to two lanes. The roadway in the opposite direction is restriped to hold five lanes of traffic and separated into a 3/2 lane configuration by a static barrier to give a total of four lanes into the city and three lanes out.
When the works restart this April, the five-lane side of the road will change dynamically from a 3/2 to a 2/3 configuration each day by using the road zipper. This will provide four lanes of traffic in the peak direction at all times and so mitigate traffic congestion out the city for the evening commute.
Across in the US, near Boston, every traffic manager’s nightmare was becoming reality as several giant potholes opened up in the deck of a bridge on the I-93, meaning it had to be closed for days for emergency repairs. Worse was to follow as surveys revealed a further 14 bridges along the route required major rehabilitation. So MassDoT decided to complete the reconstruction of all 14 bridges over 10 weekends.
Having prefabricated the bridge superstructure offsite, local roads beneath the bridge were closed at 6pm on Friday. At 8pm the zipper created crossovers to move all traffic crossing the bridge to the other side of the highway. The BTM moved the barrier out by two lanes to create a 2/2 traffic pattern, provide barrier protection between the traffic directions and create a clear channel to guide motorists through the construction zone.With the traffic control in place, the damaged bridge deck was removed and replaced with the prefabricated sections, and quick-drying concrete used to ensure that the road would be ready for Monday traffic. By 5am on Monday morning, the moveable barrier was returned to the side of the road as all lanes in both directions were reopened.
Tunnel tragedy
Just outside Tokyo, the Joban Expressway runs through a series of tunnels where parks have been built across the top of the roadway. During a project to reseal the upper interior of these tunnels, a vehicle passed through the plastic delineation separating the work zone from the live lanes and a maintenance worker was struck and killed. To prevent any further incidents, 5.8km (3.6miles) of moveable barrier has been installed but rather than being a continuous wall, operating agency (Nexico) specified four 30m (100ft) gaps for incident management.
Each night the work zone is expanded to create a larger working space, increase productivity and enhance safety. Every morning the barrier is repositioned in a double move that gives one lane back to traffic at 4am and then another at 7am. A single BTM makes the first transfer, and then drives back through the work zone to do the second move.
Barrier basics
Adjacent barrier sections are held together with a pinned pivot (secured with a circlip) allowing the assembly of any length of barrier and also enabling it to be used on radii of 118m (250ft) and above. At least 80 sections need to be deployed either side of the point where minimal deflection is required or, alternatively, this can be reduced to 30m (98ft) with anchored ends. With those requirements satisfied, a 2t vehicle travelling at 100km/h (62mph) and impacting the barrier at 25º will cause a deflection of 700mm.