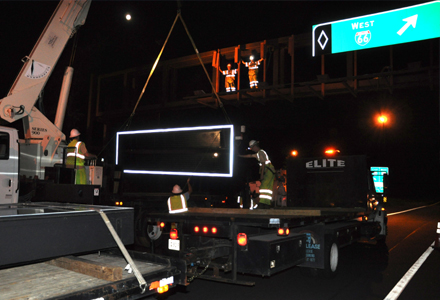
Virginia DoT faced a challenge common to many highway authorities around the world: the need, in economically challenging times, to replace ageing variable message signs reaching the end of their operational life
While many of the older VMS have been kept operational by such creative maintenance methods, VDoT recognised that even this approach was becoming unworkable. So these old signs would have to be replaced. But it is not that simple, as VDoTProject:
Virginia DoT Variable Message Sign Retrofitting programme
Cost:
$100,000 per sign approx.
Savings:
$200,000 per sign. Eventually, up to $300,000 per year savings in electrical energy and long term maintenance costs Operations & Security Division administrator Tom Phillips explains: "A replacement VMS requires a full engineering evaluation, including determination of the condition and suitability of the support structure.
This is necessary because introducing a new VMS to existing supports introduces the possibility of overload or instability due to the change in the sign from the original design," Phillips says, adding that, in Virginia, support structures are examined in the same fashion as highway bridges for keeping in good repair.
The evaluations revealed no issues with the sign gantries - all were in good health. So VDoT could focus on just replacing the VMS units. Then it hit upon an idea: What if the existing VMS could be retrofitted with new technology while retaining the sign cases and other structural elements? This approach was explored with an evaluation process which eventually lasted a year. It began with a review and proofing of available technology and a trial of implementing new sign materials within refurbished VMS sign cases.
A site was selected that was representative of an older VMS within Virginia's Northern Region near Washington, DC. The sign was removed from the support structure and a manufacturer was selected to fabricate retrofit kits that could be installed by VDoT staff or its ITS maintenance contractor.
The company chosen to carry out the work used the existing VMS components as a template for sizing replacement modules. The resulting prototyped kit configured of the company's standard products, but fitted to bespoke sign attachment hardware specifically fabricated for the existing sign.
The VMS cabinet was refurbished in an off-site location using finishes that are designed to last for many years and give the VMS a 'like new' appearance to the travelling public.
The refurbished sign was delivered and installed back on the gantry it had been removed from, then subjected to operational tests through the regional ITS control centre's advanced traffic management system. Additional tests were conducted by exposing components to environmental and proof of performance testing that validated the kit's ability to operate in the harsh environment of Northern Virginia while providing reliable messages to the motoring public.
Sign structures were inspected by VDoT with remediation made prior to the re-installation process.
Existing electrical and communication cabling was removed and replaced with new cabling, connections and power service using the existing raceway.
Because of the off-site techniques that were used for refurbishment, safety was increased and the impact to travellers minimised.
After testing and evaluation of the prototype kit as installed in the refurbished VMS sign case, the contractor refurbished 15 additional signs in the same manner from units VDoT nominated as candidates for retrofitting. These were representative of different vendors' products and sign configurations supplied over the years.
VDoT's approach to retrofitting its old VMS has been an unqualified success: additional retrofits are under contract and by year's end 2011, VDoT is expecting nearly 100 existing signs to have been refurbished.
Cost analysis
From the prototyping to the current projects that are deploying retrofitted VMS in Virginia, it was expected that there would be considerable cost saving in time and expense. Based on the estimated $300,000 per site cost for new signs, installed on new structures, the retrofitted cost is approximately $100,000. The prototyping process took approximately one year. The cost to the DoT for engineering was essentially zero as the work necessary to revise electrical power services and other field elements incidental to the retrofit were included in the contractor's price for retrofitting the signs.The new signs used the latest technology that provides improved visibility and approximately 50% reduction in power consumption.
Additional savings are realised by minimising the maintenance required to support these 'like new' VMS.
Based on the success of the programme it is expected that many more VMS signs will be retrofitted within the next few years with cost savings of around $200,000 per sign compared to traditional replacement. In addition, this programme is expected to save the DoT approximately $300,000 per year in electricity and maintenance costs.